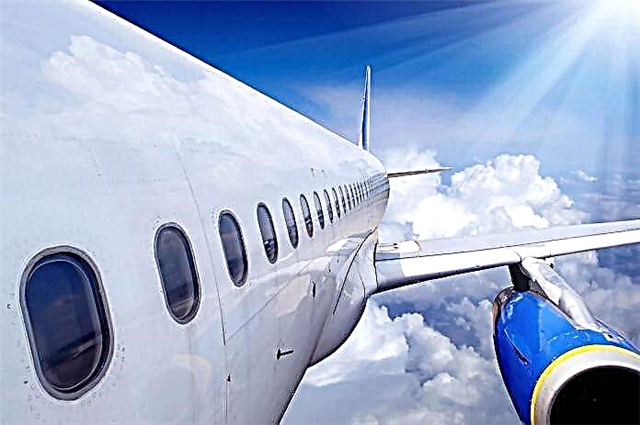
The windows of the aircraft are called portholes. Many people are wondering why this form was chosen? Indeed, in the windows of houses, in cars, square, rectangular windows are successfully used. What is the difference, is such a choice random?
It turns out that round portholes are used in aircraft construction for a reason. The practice itself dictated the need for people to dwell on just such a form.
Aircraft portholes until the 50s
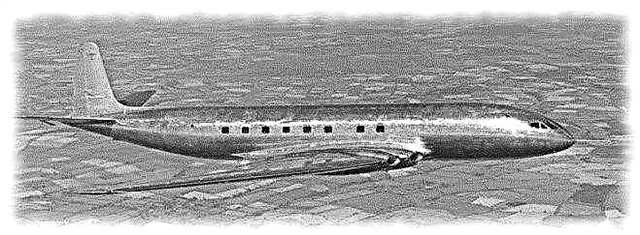
At the dawn of the aircraft industry, rectangular portholes were really used, more reminiscent of the windows of modern cars. They did not cause any problems until the 50s, before the start of the jet era in the aircraft industry. The first experiments in this direction were made in Britain, where they created an airliner called Comet - already jet, but with old rectangular portholes. It was an exceptional aircraft for its era.
Interesting fact: The Comet airliner had a pressurized cabin and other indicators unique to that time. But by 1954, two aircraft of this series simply collapsed in flight, which necessitated a review of their characteristics and device features.
Why did the Comet aircraft suffer?
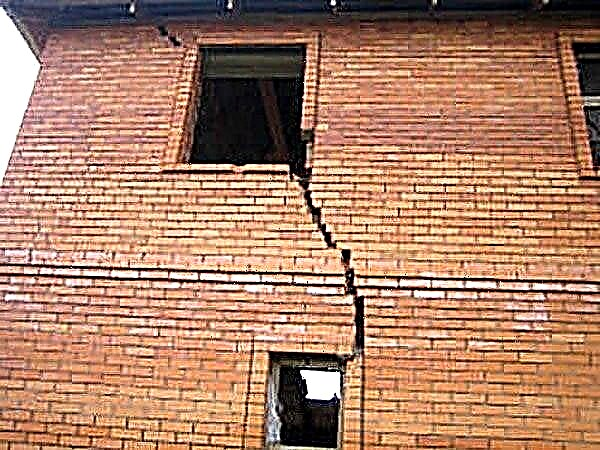
A window in the shape of a rectangle or square has four weak points, which are located just at the corners. If you put any significant physical stress, for example, a house with ordinary rectangular windows, you will notice that the cracks will come from the corner parts of the windows, and only then they will begin to spread to the entire structure.During takeoff, during the flight, very significant loads also fall on the plane. During flight, the pressure inside the aircraft’s hull is as much as 3 times higher than the pressure on the outside; during landing, the pressure on both sides of the hull is equalized. Temperature hikes also affect the airplane’s hull, which cause small changes in the hull’s dimensions.
As a result, in the presence of square or rectangular windows in the corner parts, the so-called metal fatigue accumulates, they become fragile, vulnerable. This leads subsequently to metal ruptures in these places.
This is exactly what happened with the Comet aircraft. Initially, designers and experts were at a loss, could not find the cause of the problems. In the future, when multiple pressure drops were simulated in the laboratory, it was found that the casing from this began to burst, while the gaps came just from the corners of the window.
Under the influence of external factors, small gaps, cracks in the fuselage quickly expand, the body of the aircraft literally breaks into pieces, which happened with the two sides of the Comet series. A weak spot leading to accidents was discovered.
Development of round portholes for aircraft
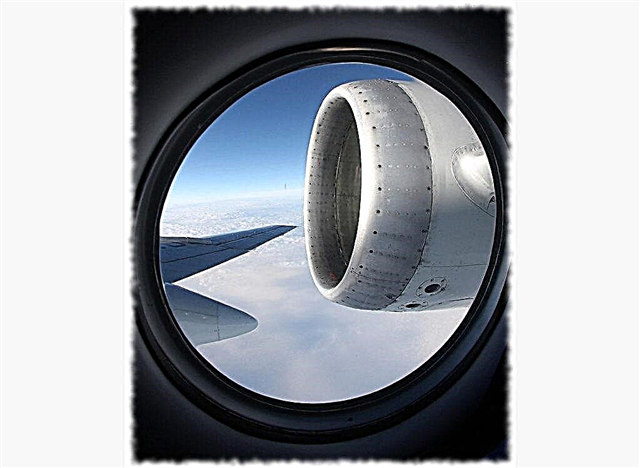
Next, experiments were conducted on the first sides with rounded portholes of a modern type. Repeated repetitions, various tests clearly showed that such a problem does not arise with them. Rounded constructions have taken root in the aircraft industry, they are used to this day, as they do not create additional risks, relieve dangerous situations, and fully justify their use.Modern airplanes fly even faster than Comets, they experience more significant overloads, but the hull successfully withstands them - largely due to the round portholes.
Rounded portholes evenly distribute the load attributable to them, do not have the ability to concentrate it at certain points. In addition, when choosing round shapes, it is easier to ensure cabin sealing, which is absolutely necessary when considering modern speeds and the height of flight of air transport.
Today, aircraft use glass with a special bend, with a carefully calibrated composition, which defend the safety of passengers and crew. They not only do not transfer concentrated load to the body, but also have protection against the risk of cracks and other damage on their surface.
Thus, the round shape of the portholes of the aircraft was not chosen by chance. It eliminates the risk of accidents, does not concentrate the load on the case. Practice has shown that at the corners of rectangular or square windows, the load is concentrated, these places are subject to increased wear, in the future - deformation, tearing. During the flight, this can lead to an accident, depressurization of the cabin, and rupture of the body metal.
Round portholes have shown themselves well in practice, they do not create additional risks, therefore they are actively used in the aircraft industry. The practice of their application has been over 60 years. Designers do not need to change this solution, it is chosen correctly.